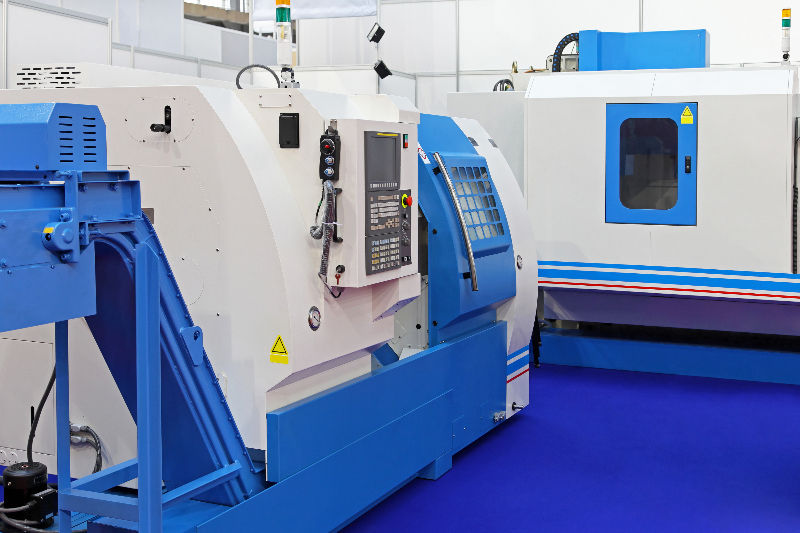
CNC (Computer Numerical Control) machines are the backbone of modern manufacturing, powering everything from intricate aerospace components to automotive parts. But like any complex machinery, they require regular maintenance and timely repairs to ensure they continue running at optimal performance. This is where expert CNC service engineers and machine repair solutions come into play. In the UK, these professionals provide a wide range of critical services to keep CNC machines running smoothly, ensuring manufacturers avoid costly downtime and expensive repairs.
Types of Services Provided by CNC Service Engineers
1. CNC Machine Maintenance & Calibration
One of the core services offered by CNC engineers is routine maintenance, including the calibration of CNC machines. These professionals ensure that every part of the machine operates according to factory specifications, preventing errors in production and reducing the risk of breakdowns. Regular calibration guarantees that parts are manufactured with the necessary precision.
2. Preventive Maintenance Programs
Many CNC service companies offer tailored preventive maintenance programs, which help manufacturers proactively maintain their equipment. These programs typically involve scheduled checks, lubrications, software updates, and part replacements. Preventive maintenance is crucial for avoiding unexpected breakdowns and increasing the longevity of machines.
3. CNC Machine Troubleshooting and Repairs
CNC machines are intricate systems that involve electrical and mechanical components working together. When a machine breaks down, diagnosing and fixing the issue promptly is essential. CNC service engineers are skilled at troubleshooting and repairing common problems like electrical failures, misalignments, faulty motors, or software glitches. Quick resolution of issues minimizes downtime and prevents further damage to the machinery.
4. Electrical and Mechanical Troubleshooting
CNC machines require both electrical and mechanical expertise to resolve issues. Service engineers are equipped to handle everything from electrical malfunctions, such as faulty wiring or sensor issues, to mechanical problems like misaligned parts or malfunctioning motors. Prompt troubleshooting and repairs ensure that operations are back on track without significant delays.
5. CNC Machine Installations and Upgrades
As technology evolves, businesses may need to upgrade their CNC machinery to improve efficiency and productivity. CNC service engineers are skilled in machine installations and can handle the setup, calibration, and integration of new equipment. They can also assist with retrofitting older machines with modern controls and software, extending the life of valuable equipment.
6. Emergency Repairs and Support
Despite best efforts with maintenance, breakdowns are sometimes inevitable. Expert CNC service engineers are available for emergency repairs to minimize downtime. Whether it's a mechanical failure, software glitch, or electrical issue, these professionals are equipped to resolve the problem quickly and get machines back in action.
7. Spindle Repairs & Overhaul
Spindles are at the heart of CNC machines, driving the cutting tools that shape and refine raw materials. Over time, spindles experience wear and tear, leading to reduced performance, overheating, or complete failure. CNC service engineers specialize in spindle repairs, bearing replacements, rebalancing, and complete spindle overhauls to restore full functionality. Timely spindle servicing helps prevent vibration issues, accuracy loss, and costly unplanned downtime.
The Importance of Planned Maintenance for CNC Machines
Preventing Unexpected Breakdowns
One of the most significant advantages of planned maintenance is the ability to anticipate and address issues before they lead to breakdowns. Without proper care, a minor fault can escalate into a full-blown machinery failure. Regular inspections and servicing identify early signs of wear and tear, helping prevent costly emergency repairs.
Minimizing Production Downtime
Production downtime can have a severe impact on a manufacturing business, leading to delays, missed deadlines, and financial losses. Planned maintenance helps reduce the risk of unplanned downtime, ensuring CNC machines run reliably. By scheduling service during off-peak times, manufacturers can maintain high productivity levels without the risk of sudden interruptions.
Extending the Life of CNC Machines
CNC machines are significant investments, and manufacturers aim to maximize the lifespan of their equipment. Regular maintenance ensures that machines are running at peak performance, preventing excessive wear and tear that could shorten their operational lifespan. By identifying potential issues early, businesses can address them before they cause irreversible damage.
Improving Accuracy and Quality
CNC machines are designed to produce highly precise parts, but even small misalignments can result in defective products. Scheduled maintenance ensures that the machine’s components are in top shape, allowing for consistent quality and high-precision outputs. This is particularly crucial in industries like aerospace and medical manufacturing, where accuracy is paramount.
Reducing Repair Costs
While regular maintenance involves an upfront cost, it can save manufacturers money in the long run by preventing expensive, large-scale repairs. Addressing small issues early helps to avoid more significant failures that require costly repairs or even machine replacement.
Enhancing Operational Efficiency
A well-maintained CNC machine operates more efficiently, consuming less energy and reducing unnecessary strain on components. This efficiency translates into cost savings, improved production rates, and lower overall operational costs.
Conclusion
The importance of expert CNC service engineers and machine repair solutions cannot be overstated. With their expertise, manufacturers can keep their machinery running at peak efficiency, avoid unplanned downtime, and reduce the risk of expensive repairs. Planned maintenance plays a vital role in maintaining the longevity and precision of CNC machines, ensuring that manufacturers can continue producing high-quality products without interruptions. Investing in professional service and preventive maintenance is the best way to protect your machinery, your production line, and your bottom line.
If you're looking for a top-class subcontract service engineer to handle your CNC machine needs, Manufacturers Hub is the perfect place to connect with skilled professionals. Our platform allows you to find the ideal service engineer who will provide expert, reliable support tailored to your specific requirements.